更なる微細化に向けた加工条件最適化技術
- HOME
- 更なる微細化に向けた加工条件最適化技術
当社の強み 4つのオンリーワン技術
臨機応変に幅広い分野で活用可能な「放電加工」は、複雑微細形状の創生に必要不可欠な技術であると考えています。
狭ピッチコネクターなど、放電加工対象断面積が0.1㎟以下で顕微鏡でしか確認できないような複雑微細形状で寸法公差0~-0.002㎜を満足するような多数個取り対応のクリアランス0.02㎜以下の最適加工条件は、もともと存在しておらず、必要に応じてその都度自作対応しなければなりません。
世に言う「匠の業」や「職人業」的な技法が要求される世界なのです。
微細工具 非接触 機上成形技術
わが国でしかできない究極のものづくりを実現するため、軽薄短小商品を最短で市場に供給することが求められています。
当社は微細加工用新加工技術の開発を行い、微細化対応、新素材対応を軸とした安易な設備投資では追従不能なオンリーワン技術を多数保有しております。
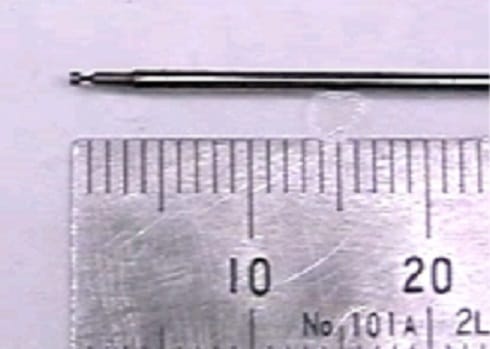
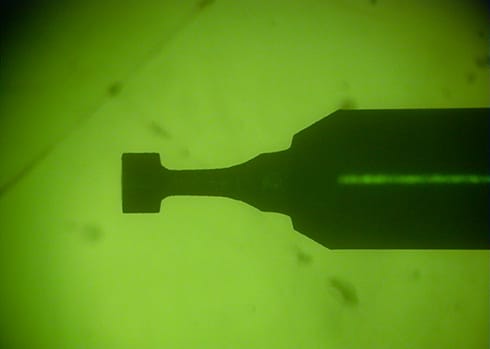
例えば、上の2枚の写真は銀タングステン合金電極でΦ1×50Lの先端部3.5mmを機上成形により、中グリ加工用の段付き電極形状にドレッシングしたものです。
先端部はΦ0.274×t0.182でそれを支える軸径はわずかΦ0.080mmしかありません。
この工具電極をスリット幅0.500mmの中に深さ0.0635mmより奥をR0.1525に中グリ拡大追加工するための工具として複数回、成形⇒加工を繰り返します。
中グリ加工した内面のインコーナーRに公差があり、R0.0375±0.0025という厳しい要求公差を満足する必要があります。
精度検査法として、当社では使用後の工具電極を寸法測定し、放電ギャップを加味した仕上がり寸法データ予測法を採用しています。
このような顕微鏡測定を挟んだ自作電極の繰り返し成形法による職人業的技法は、自動化・無人化対応が難しく、技能の伝承が課題とされていますが、当社では、幅広い実践加工を通じて、各人各様在籍年数に応じた経験知を基にした取り組みを重んじており、個々人の自主性に任せる手法でスキルアップを図っております。
次世代微細加工技術
1.高速レーザ加工技術
工具レス高速レーザ加工技術により高効率な加工が非接触で行えることが特徴です。
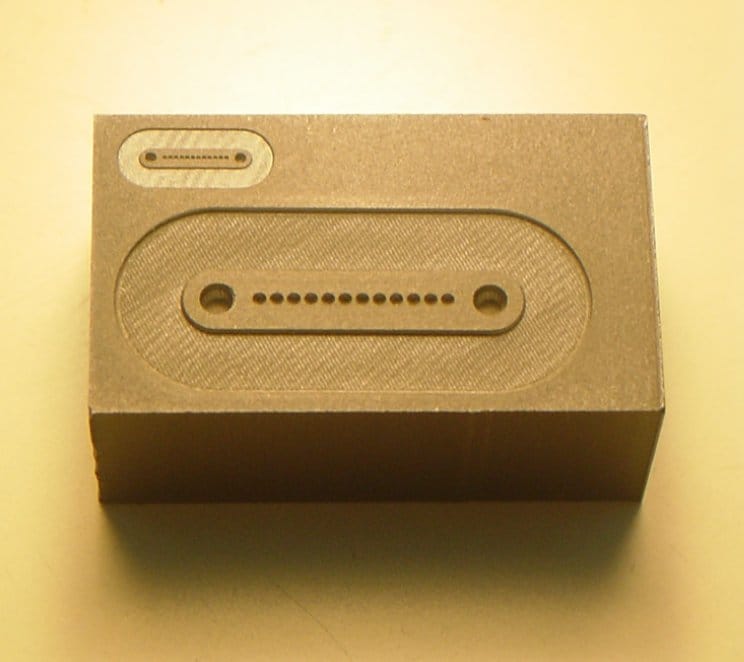
マイクロレンズアレイ用Sic金型
【詳細説明】
12-φ0.200×深0.100の半球状の彫り込みをビームスポット径φ0.03のレーザ形彫り加工機にて工具レスで高速加工後、ダイヤモンドコーティングされたボールエンドミルで高品位面仕上
【材質】
SiCセラミックス500~600℃の熱間プレスで成形されるガラスレンズは、従来の超硬合金にDLCコーティングされた金型では熱膨張による剥離が生じやす型寿命が著しく短いことが課題でしたが、SiCセラミックス製金型は高温強度や離形性に優れ、長寿命化が図れます
【サイズ】
左上が実寸、下側は3倍拡大モデルです
2.高精度放電加工技術
微細電極成形技術および高精度放電加工技術により超精密化対応が可能です。
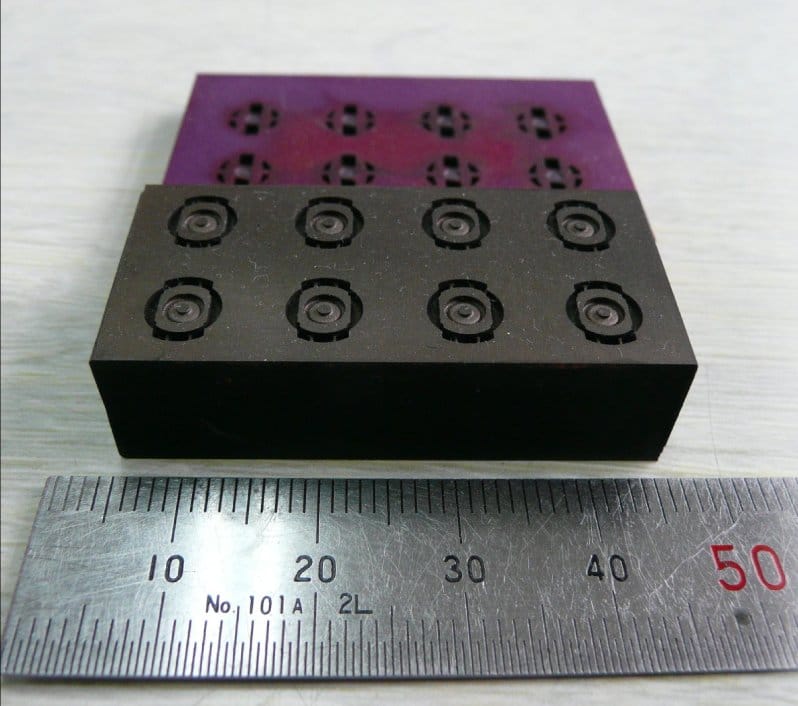
スイッチング素子用セラミックス金型
詳細説明】
レーザでは追従不可能な高アスペクト比の微細な異形深穴を複数の銅タングステン合金製電極を用いて精密転写する手法で独自の形彫り放電加工技術により追加工しています
【材質】
SiC(炭化ケイ素)
【サイズ】
20×40×15
3.高品位超音波仕上技術
放電加工でダイヤモンド工具を任意形状に成形し、機上で超音波仕上げする技術を確立しました。
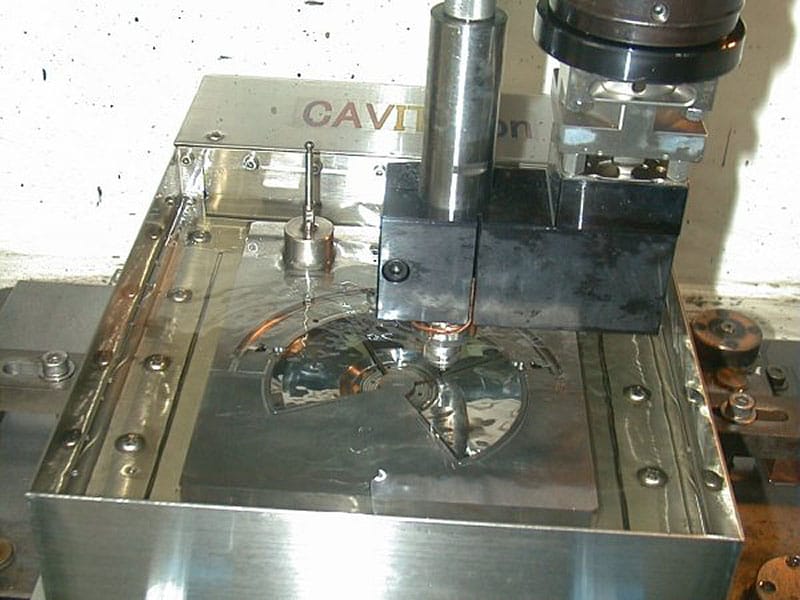
クマクラ製超音波加振浸漬装置 CAVITT
【詳細説明】
28kHz、振動振幅1~6μmの超音波振動水槽付きテーブル。
テーブルサイズは200×200×60
ナカニシ製増速スピンドル NR-3060S
詳細説明】
主軸回転速度5,000~60,000min-1 エロワ高精度脱着仕様
放電加工機上にセットし、ダイヤモンド工具を放電成形し、切削や研削モードでスキャニングする際、既存のスピンドルでは回転数不足のため本増速スピンドルを付けて高速旋回させながらミーリング加工を行えるもので、工具の摩耗があれば自動で再ドレッシングを繰り返すことで超精密仕上げが可能となる画期的なシステムです。
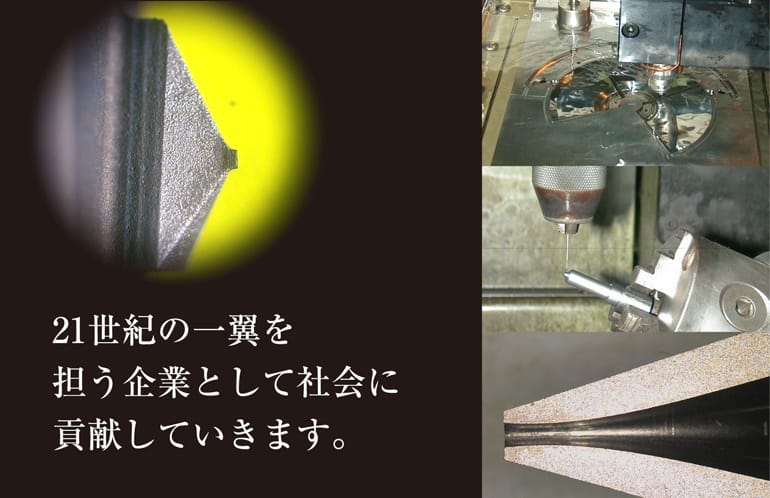