2024/09/12
放電加工による微細加工とは
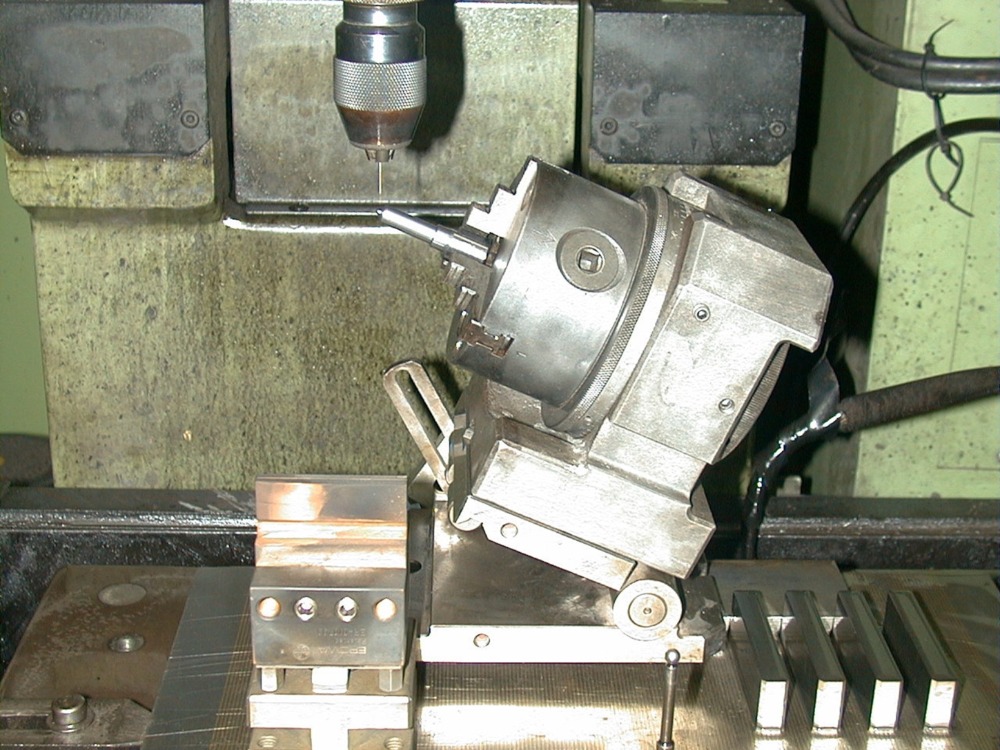
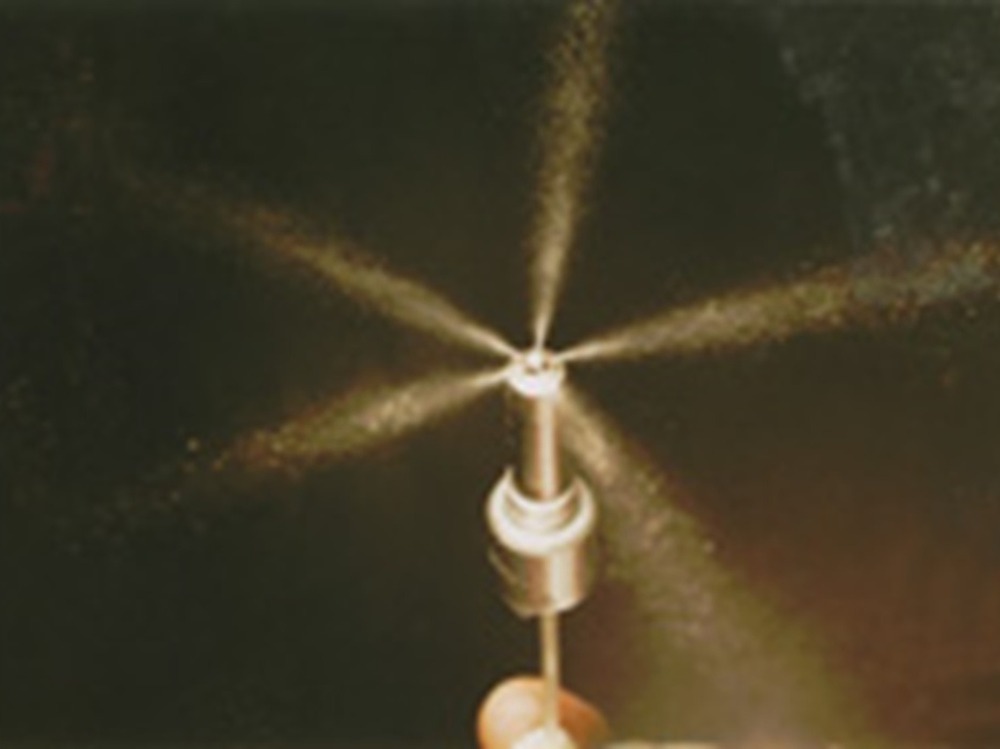
放電加工による微細加工とは?事例の紹介
放電加工とは、電気エネルギーを利用して金属を溶融除去する加工方法であり、特に硬度の高い材料や複雑な形状の加工が求められる場合に効果的です。微細加工とは、非常に小さなスケールでの加工技術を指し、高精度が求められる分野で頻繁に利用されます。放電加工は、微細加工の一つの方法として、外科手術器具や精密部品の製造において大きな役割を果たしています。特に、微細加工とは何かを考えるとき、工具を工作物に強引に押し付ける力づくの工法ではなく、非接触で最も力のかからない工法ゆえ、放電加工はその代表的な手法といえます。微細加工とは、ただ小さくするだけでなく、非常に高い精度と品質を保ちながら、特定の機能や性能を実現することを意味します。放電加工を用いた微細加工の事例として、非常に微小な孔を開ける技術や微細な溝を形成する技術があります。これらは半導体製造や医療機器の製造など、多岐にわたる分野で活用されています。
微細加工技術の基礎
微細加工技術の基礎は、非常に小さなスケールでの正確な加工を実現するための技術体系です。この技術は、電子デバイス、医療機器、光学機器など、さまざまな分野で不可欠となっています。微細加工技術は、極めて高い次元の精度と制御を要求されるため、特殊な装置と高度な技術が必要です。微細加工技術の中でも代表的な方法として、放電加工やレーザー加工があります。これらの技術は、それぞれの特性を活かした異なる加工方法を提供します。基礎として知っておくべきポイントは、材料特性、加工方法、装置の選び方、そしてプロセス制御です。例えば、半導体製造では微細加工技術が欠かせない要素であり、ナノメートル単位の加工精度が必要とされます。微細加工技術の基礎を理解することは、これらの高度な応用を実現する上で非常に重要です。
微細加工とは
微細加工とは、非常に小さなスケールでの物体の加工を指し、その定義はマイクロメートルからナノメートルの範囲を含みます。具体的な意味は、材料の表面や内部に微小な形状や構造を形成する技術です。微細加工技術は、エレクトロニクス、バイオテクノロジー、光学機器などの分野で不可欠です。微細加工とは数ミクロン以下の寸法で、極めて高い精度と制御が求められるため、高度な技術と専門的な装置が必要とされます。例えば、半導体チップの製造では数ナノメートル単位の微細加工が行われています。微細加工とは、ただ物を小さくするだけでなく、その精度や品質を保ちながら特定の機能や性能を実現することを意味します。この技術は、製品の高性能化や新しい機能の開発に寄与している重要な技術です。
微細加工技術 半導体における役割
微細加工技術は、半導体製造において極めて重要な役割を果たしています。半導体チップの製造では、ナノメートル単位の精度が求められ、微細加工技術がその精度を実現します。微細加工技術は、高密度回路の形成やトランジスタの微細製造に利用され、これにより半導体の性能が劇的に向上します。微細加工技術には、フォトリソグラフィー、エッチング、化学気相成長(CVD)などが含まれます。これらの技術は互いに連携して、極めて高い精度の加工を可能にします。例えば、フォトリソグラフィーは光を用いて微細なパターンを形成し、CVDは薄膜を材料表面に堆積させます。半導体業界では、微細加工技術の進化が新しい世代のデバイスの開発を支え続けています。これにより、高性能で小型なデバイスが市場に供給されることが可能となります。
放電加工の応用
放電加工は多岐にわたる分野でその応用がなされています。その主な特徴は、硬度が高く、従来の機械加工では困難な材料でも加工できる点です。航空宇宙産業では、エンジン部品やタービンブレードの微細加工に広く利用されています。また、医療分野では、手術用インスツルメントや義肢の高精度な部品製造にも使用されています。このように、放電加工の応用範囲は非常に広く、精度が要求される先端技術分野でもその重要性が増しています。精密金型の製造でも放電加工技術は不可欠であり、高い再現性と微細な加工が可能です。さらに、自動車産業でも高強度材料の加工や、エンジン部品の高精度な製造に役立っています。これにより、放電加工は、製品の性能向上や新しい設計の実現に寄与しています。
放電加工とは
放電加工とは、電気エネルギーを利用して金属を溶融除去させる加工方法です。その仕組みは、電極と工作物の間に電圧をかけて放電を発生させ、その放電エネルギーで材料を加工する点にあります。放電加工は非接触加工であり、電極と工作物が直接接触しないため、非常に高精度な加工が可能です。さらに、硬度が高い材料や複雑な形状でも加工できる点が特徴です。このため、航空宇宙、医療、自動車など、多くの産業で利用されています。電極の形状を変えることで多様な形状加工が可能で、微細加工や極めて高精度な製品の製造に最適です。放電加工の具体例としては、金型、精密部品、微細穴の作成などが挙げられます。これにより、放電加工は従来の切削加工では困難なタスクにも対応できる、高度な加工技術といえます。
放電加工の具体例
放電加工の具体例としては、精密金型の製造が挙げられます。この技術を用いることで、複雑な形状や微細なパターンを高精度に加工することができます。例えば、自動車部品や電子機器のための細かな金型は、放電加工によって実現されています。また、医療器具の分野でも、ステントやミクロサイズの手術用道具など、極めて繊細な加工が必要な製品が多数存在します。これらも放電加工の技術によって製造されています。さらに、航空宇宙産業ではタービンブレードやエンジン部品といった高強度材料の加工にも放電加工が利用されています。これにより、耐久性と精度が求められる部品が製造され、各産業の技術革新に貢献しています。放電加工は、こうした多様な分野でその強みを発揮し、材料の選択肢を広げることで、新しい応用を可能にしているのです。
微細加工機と放電加工機の違い
微細加工機と放電加工機は、どちらも高精度な加工が可能な装置ですが、用途や原理に違いがあります。微細加工機は、主に切削や研削、レーザー加工などを利用して微細な部分を加工するための装置です。これに対し、放電加工機は電気エネルギーを利用して金属を溶融除去させる方法で加工を行います。微細加工機は、材料の除去速度や加工精度において高い性能を発揮し、ミリメートル以下の精度での加工が可能です。一方、放電加工機は、硬度の高い材料や複雑な形状の加工に適しており、非接触での高精度加工を実現します。両者の違いは、加工方法とその用途にあります。例えば、航空宇宙や医療分野での高精度部品の製造には、両者の特性を活かした適切な装置の選択が不可欠です。
微細加工方法の種類
微細加工方法にはさまざまな種類があり、それぞれに特有の利点と適用分野があります。代表的な方法として、切削加工、マシニング、レーザー加工、ワイヤー放電加工などが挙げられます。これらの方法は、求められる加工精度や材料の特性に応じて使い分けられます。例えば、切削加工は金属や樹脂の精密な表面加工に適しています。一方、レーザー加工は高熱を利用した非接触加工で、極めて高い精度が必要な場合に効果的です。ワイヤー放電加工は、硬度が高く複雑な形状の加工に適しています。これらの微細加工方法の選択は、製品の品質や性能を左右するため、非常に重要です。
切削による微細加工方法
切削による微細加工方法は、主に工具を用いて材料の一部を削り取る技術です。この方法は、高精度の加工が可能であり、金属、プラスチック、セラミックスなど多様な材料に対応しています。特に、工具の形状や材質を調整することで、極めて精密な加工が実現します。切削加工の代表的な機械としては、旋盤、ミリングマシン、ドリルなどがあります。これらの機械は、微細な形状を高い再現性で加工することができるため、自動車部品や医療機器の製造において重要な役割を果たしています。また、高速切削技術の導入により、加工速度と仕上げ精度が向上し、生産効率を大幅にアップすることが可能です。切削による微細加工方法は、材料特性に合わせた最適な工具選択と加工条件の設定が求められる技術です。
マシニングの特徴とその応用
マシニングは、切削工具を用いて材料を高精度に加工する技術です。この技術は、複雑な形状を持つ部品や微細な部分の加工に特化しています。マシニングの特徴としては、高速での加工が可能であり、精度も非常に高い点が挙げられます。さらに、コンピュータ数値制御(CNC)を取り入れることで、複雑なプログラムに基づく精密加工が実現します。マシニングの応用分野は広く、自動車産業や航空宇宙産業、医療機器の製造など、多岐にわたります。特に、エンジン部品やタービンブレード、医療用インプラントなど、高い精度が求められる製品の加工に適しています。また、マシニングセンターなどの多軸機を用いることで、複雑な3D形状の加工も可能になります。この技術は、製品の品質向上と生産効率の向上に貢献しています。
レーザーを用いた加工技術
レーザーを用いた加工技術は、光のエネルギーを利用して材料を加工する先進的な手法です。この方法は、高い精度と速度で材料の切断、溶接、表面改質を実現します。レーザー加工は非接触加工であり、工具の摩耗がないため、長期間安定した加工が可能です。また、微細なパターンや複雑な形状の加工も容易に行える点が特徴です。たとえば、電子デバイスの基板加工や精密機器の部品製造など、高度な精度が求められる分野で広く活用されています。さらに、レーザー加工は金属のみならず、プラスチックやセラミックスなど多様な材料に対応しています。加工中に発生する熱の影響を最小限に抑えることができるため、材料の変形や熱影響を防ぐことが可能です。これにより、レーザーを用いた加工技術は高精度かつ高効率な製造方法として、さまざまな産業で利用されています。
ワイヤー放電加工の詳細
ワイヤー放電加工は、電気エネルギーを利用して金属を微細に加工する技術です。この方法では、導電性のあるワイヤーを電極として使用し、工作物との間に放電を発生させて材料を溶融除去します。ワイヤー放電加工は、硬度が高く、従来の切削加工では困難な材料に対しても有効です。特に、微細な溝や複雑な曲線、内部の穴など、従来の加工方法では難しい形状の加工が可能です。この技術は、航空宇宙、医療、自動車など、精度が求められる部品の製造において重要な役割を果たしています。また、ワイヤーの直径を微細にすることで、非常に高い精度での加工が実現します。さらに、非接触での加工が行えるため、材料表面にダメージを与えずに加工を行うことができます。これにより、ワイヤー放電加工は、精密かつ高品質な加工が求められる製品に対して非常に適した技術といえます。
高精度な微細加工の実現
高精度な微細加工は、製品の性能向上や新しい技術の開発において非常に重要です。高い精度を達成するためには、様々な要素が密接に関連しています。温度管理、機械の振動対策、使用する装置および測定機器の精度など、多くの要因が高精度な加工に影響を与えます。これらの要素は、加工の結果に直接反映されるため、厳密に管理しなければなりません。以下では、それぞれの要素に焦点を当てて具体的に説明します。
精度と温度管理の重要性
微細加工において、高精度を維持するためには温度管理が欠かせません。加工中の温度変動がわずかでも、精度に大きな影響を与えることがあります。例えば、微細な寸法変化や材料の熱膨張が原因で、加工精度が低下する可能性があります。このため、加工環境の温度を一定に保つことが重要です。空調設備の導入や温度センサーを使用してリアルタイムで温度を監視することで、温度管理が実現できます。さらに、装置自体にも温度を最小限に抑える冷却システムが搭載されていることが望ましいです。こうした温度管理対策を徹底することで、微細加工の精度を高いレベルで維持することが可能となります。
機械の振動対策とその影響
機械の振動は、微細加工の精度に大きな影響を与える要因の一つです。加工中に発生する振動が制御されないと、工具の位置が微妙にずれたり、加工面が不均一になることがあります。これを避けるためには、振動対策が不可欠です。具体的には、防振台の使用や加工機の剛性を高めることで、振動を最小限に抑えることができます。さらには、振動センサーを取り付けてリアルタイムで振動を監視し、必要に応じて自動的に振動を減少させるシステムも導入されています。これにより、微細な加工精度が一貫して保たれることが確保されます。振動対策を適切に行うことで、高い品質の微細加工が実現可能となります。
使用する装置と測定機器の精度
微細加工において使用する装置と測定機器の精度は、加工結果を左右する重要な要素です。まず、使用する加工装置は高い精度を持っていることが必須です。これにより、微細な寸法や形状が正確に再現できます。また、加工後の測定に使用する機器も、同様に高精度である必要があります。例えば、座標測定機やレーザーマイクロメーターなどの高性能な測定機器を使用することで、加工後の製品が設計通りであるかどうかを確認できます。これにより、品質管理が一層厳密に行えます。さらに、定期的なキャリブレーションを行うことで、装置や測定機器の精度を維持することができます。こうした取り組みを通じて、高精度な微細加工が安定して実現されます。
微細加工製品の事例紹介
様々な微細加工製品の事例を紹介します。微細加工技術は、半導体や医療機器、自動車産業など、多岐にわたる分野で応用されています。その精度と効率性が求められるため、各分野での実際の製品には非常に高い品質が求められます。例えば、微細穴加工、微細溝加工、複雑な形状の部品加工などが挙げられます。このような製品は、それぞれの用途に特化した高性能な微細加工技術によって製造されます。具体的な事例に目を向けることで、微細加工がどのような形で実現されているか、その具体的な応用を理解することができます。
半導体向けの微細穴加工
半導体向けの微細穴加工は、極めて高い精度が求められる技術です。特に、半導体チップや電子回路基板には微細な孔が数多く必要とされ、その製造には精密な加工技術が不可欠です。レーザー加工や放電加工などが主に用いられ、これによりナノメートル単位の高精度な穴あけが可能となります。また、微細穴加工は、電子部品のスルーホールやボンディングパッドの形成においても重要な役割を果たしています。このようにして製造された半導体製品は、より高性能で小型化が進み、現代の電子機器に欠かせない要素となっています。材料の選択や加工条件の最適化も極めて重要であり、これにより微細加工の品質と信頼性が高まります。
SUS材を用いた微細溝加工
SUS材を用いた微細溝加工では、主にステンレス鋼を対象とした高度な加工技術が求められます。ステンレス鋼はその耐久性と腐食抵抗性に優れるため、医療機器や食品機械、化学工業製品などさまざまな分野で採用されています。微細溝加工は、レーザーやエッチング技術を用いてステンレス鋼表面に非常に小さな溝を形成するプロセスです。これにより、流体の流れを制御したり、表面の付着性を改良したりすることが可能になります。例えば、微細溝加工は医療機器のカテーテルや内視鏡の部品製造に応用され、加工精度が求められます。高い加工精度の確保には、温度管理や振動対策、使用する装置の適切な選択が不可欠です。これにより、微細溝加工の品質と信頼性が大幅に向上します。
産業用途の微細加工製品一覧
産業用途の微細加工製品一覧には、さまざまな分野における精密加工部品が含まれます。これらの製品は、特定の用途に応じて高度な技術を駆使して製造されています。まず、航空宇宙産業では、エンジンブレードや高精度なタービン部品が需要されています。これらの製品は、極めて高い耐久性と精度が求められるため、微細加工技術が欠かせません。また、自動車産業では、エンジン部品やトランスミッションの微細加工が行われており、これにより車両の性能向上が図られています。さらに、医療分野においては、カテーテルやステントなどの微細かつ高精度な医療機器が製造されています。そして、電子機器の製造分野では、半導体やプリント回路基板(PCB)の微細加工が行われており、これにより電子機器の小型化と高性能化が実現されています。このように、産業用途の微細加工製品は、各分野での技術革新と性能向上に貢献しています。
微細加工の課題とその解決方法
微細加工には多くの課題が存在し、それを解決するための方法がさまざまな工業技術によって開発されています。高精度を維持するための温度管理、機械の振動防止、使用する装置の精度など、多くの要素が影響を与えます。また、材料の特性や加工後の品質管理も重要です。これら課題に対処する方法として、研磨技術の向上や最新の微細加工装置の導入が挙げられます。さらに、技術者のスキル向上も不可欠であり、トレーニングと実践的な経験の積み重ねが求められます。以下では、具体的な課題とその解決方法について詳しく説明します。
一般的な課題とその対策
微細加工における一般的な課題として、加工精度の維持、材料の選択、工具の摩耗、加工環境の制御などが挙げられます。これらの課題に対しては、いくつかの対策があります。まず、加工精度を向上させるためには、温度管理が重要です。温度変動が微細な寸法変化を引き起こすため、空調設備や温度センサーの導入で温度を一定に保つことが必要です。材料の選択では、加工しやすい材料と耐久性に優れた材料をバランスよく選ぶことが求められます。工具の摩耗に対しては、高耐久工具の使用や定期的な工具交換が有効です。最後に、加工環境の制御では、防振装置やクリーンルームの利用が考えられます。これにより、微細加工の精度と品質が向上します。
研磨技術による精度向上
研磨技術は、微細加工において非常に重要な役割を果たします。研磨技術を駆使することで、加工面の精度や仕上げ品質を大幅に向上させることが可能です。特に、精密な部品や表面の微細な仕上げが求められる場合に、研磨技術が不可欠です。たとえば、半導体ウエハーの表面研磨や、医療用デバイスの微細部品の研磨には、高度な技術が必要です。これには、ダイヤモンドペーストやセラミックバフなどの特殊な研磨材が使用されます。これにより、極めて滑らかで高精度な表面を得ることができます。研磨技術の進化により、従来の切削や削減加工では達成できなかったレベルの精度が実現されています。温度管理や振動対策と組み合わせることで、さらに高い品質の微細加工が可能となります。
最新の微細加工装置の選び方
最新の微細加工装置を選ぶ際には、いくつかの重要なポイントが考慮されます。まず、装置の精度と安定性が最優先事項です。高精度の加工を実現するためには、微小な誤差でも排除できる装置が求められます。また、装置の柔軟性も重要であり、多様な素材や形状に対応できるものが望ましいです。次に、操作性とメンテナンス性も装置選びの重要な要素です。使いやすく、メンテナンスが容易である装置は、作業効率を高めるだけでなく、長期的なコスト削減にもつながります。さらに、安全性も不可欠です。特に、高速回転や高圧加工を行う装置では、安全機能が充実していることが求められます。最後にサポート体制も確認事項の一つです。信頼できるメーカーのサポートがあることで、トラブル時にも迅速に対応できます。これらのポイントを総合的に考慮し、最適な微細加工装置を選ぶことが成功の鍵となります。
まとめ
微細加工技術は、多岐にわたる分野で不可欠な技術とされています。高精度な加工を実現するためには、さまざまな対策や技術の導入が求められる中で、温度管理や振動対策、そして最新の装置の適切な選定が重要です。これらの要素は、製品の品質や性能に直結するため、細心の注意が必要です。以下に、微細加工技術の未来と展望、そして放電加工の可能性について具体的に述べます。
微細加工技術の未来と展望
微細加工技術は、現在も進化を遂げており、今後の展望としてさらなる精度向上と多機能化が期待されています。特に、ナノメートルレベルの加工技術は、半導体や医療分野を中心に大きな進展が見込まれています。また、3Dプリンティング技術との融合も注目されています。これにより、従来は困難であった複雑な形状や内部構造の加工が可能になり、製品設計の自由度が飛躍的に向上します。さらに、グリーンテクノロジーの導入により、環境負荷を低減しながら高効率な加工が実現される方向です。これらの進化は、製造業全体の革新をもたらし、新しい製品やサービスの開発を促進します。微細加工技術は、未来の産業基盤を支える重要な技術であり、その可能性は無限に広がっています。
放電加工の可能性
放電加工は、今後さらに多様な応用が期待される技術です。この方法は、従来の切削や研削加工では対応が難しい素材や形状を高い精度で加工する能力を持っています。特に、航空宇宙産業や医療分野では、その独自の特性を活かした新しい応用が進んでいます。また、複雑な内部構造を持つ3Dプリンティング技術で積層造形された仕掛品への追加工や微細なパターンの精密加工も容易で、金型製造など高精度を求められる場面での利用が拡大しています。さらに、放電加工技術の向上により、加工速度の向上や消耗部品の寿命延長が実現されています。これにより、生産効率が大幅に向上し、コスト削減も可能になります。将来的には、自動化技術との組み合わせや新材料への対応など、さらに多くの可能性が広がることが期待されているため、放電加工は非常に魅力的な技術として注目されています。